Educational information on process control, industrial instrumentation, valves, valve automation and control valves. For additional information visit IvesEquipment.com or call 877-768-1600
Automation and Control Solutions for Hydrogen Production and Alternative Energy
100% Hygienic Tank Cleaning Coverage & Water and Chemical Savings with Alfa Laval PlusClean® Nozzle
In the food, dairy beverage farmer, and personal care industries, sufficient tank cleaning can challenge certain products. It's not just about the tank walls. Internals like agitators connections and coils can create shadow areas with a high risk of product contamination. Solving this has meant techniques like spray balls, retractable cleaning devices, or the fill and dump method. These consume time, significant cleaning media, and energy, and they compromise hygienic safety.
Alfa Laval PlusClean® makes this challenge a thing of the past. This new cleaning nozzle ensures 100% cleaning coverage, even in shadow areas. Installed flush with the tank wall it, doesn't interfere with other internals in the tank and can even be used in tanks with components close to the walls.
Activated during cleaning-in-place, PlusClean® reduces water and chemical consumption by up to 80 percent and delivers a spray pattern optimized to cover shadow areas. It thereby guarantees 100 cleaning coverage regardless of your specific tank design, while a revolutionary built-in adjustment function makes installation and operation effective and easy.
PlusClean® is available with a pneumatic driven option combined with alpha level think top for intelligent control. It also comes in an ultra-pure version with the comprehensive Alfa Laval Q-doc documentation package.
With 100 cleaning coverage, the alpha level PlusClean® cleaning nozzle eliminates risk while reducing water and cleaning media consumption. It's easy to install, simple to use, and delivers rapid payback time.
For more information, contact:
Ives Equipment
(877) 768-1600
Lead-Free Solenoid Valves
Lead is a highly poisonous substance. Manufacturers of drinking water fountains, reverse osmosis systems, coffee makers, and commercial kitchen equipment are affected by strict US safety standards. Soldering flux having a lead content of more than 0.2 percent, or a weighted average of 0.25 percent lead in the wetted surfaces of pipes, pipe fittings, plumbing fittings, and fixtures, cannot be used in a lead-free system. Lead-free is a cumulative term under the law.
As a result, Ives Equipment and ASCO offer various lead-free valve options that comply with the new rules, are NSF certified, and are available in the industry's most comprehensive range of pipe sizes, pressure or temperature ratings, and flow coefficients.
Customers can meet the safety regulations for components of purifying water systems by using reliable, readily available NSF-certified fluid control products and solutions. ASCO offers the broadest selection of pipe size, pressure or temperature ratings, and flow coefficients in the market, all of which meet the new rules.
LEAD-FREE BRASS SOLENOID VALVES
ASCO offers lead-free brass construction in their general service solenoid valves with the same proven performance, reliability, and quick availability as their brass solenoid valve equivalents.
PLASTIC AND COMPOSITE SOLENOID VALVES
Solenoid valves made of composites or plastics have the benefit of being lead-free from the outset. They come in a variety of pipe diameters and shapes, including those used in drinking water systems. For residential and commercial drinking water services, these valves are presently possibly the most popular option. ASCO offers a comprehensive selection of NSF-certified composite valves to fulfill the needs of the industry.
STAINLESS STEEL VALVES
Stainless steel, another lead-free option, provides compliance in a durable metal body. This material's valves have the most extensive range of properties in categories, including pipe size, pressure or temperature ratings, and flow coefficient in the industry (Cv).
For more information, contact Ives Equipment.
877-768-1600
https://ivesequipment.com
Don't Risk Equipment or Safety: Freeze Protect Your Plant Now
![]() |
Don't let this happen at your plant. |
Main Categories for Industrial Heat Tracing
- Industrial Pipe Tracing Cable
- Industrial Tank and Vessel Heating
- Industrial Snow Melting
- Industrial Roof Gutter Deicing
Responsible facility management includes protecting buildings and equipment against freeze damage. There are many items in any given manufacturing plant to protect, including piping systems, process instrumentation, holding tanks, transfer vessels, and valves. For each of these items, there's a good freeze protection solution to be applied. Here are some of the more common heat tracing products used in these applications.
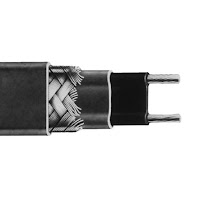
Self-regulating Heat Tracing Cable
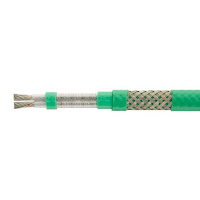
Constant Wattage Heat Tracing Cable
Constant wattage heater cable is ideal for use in maintaining fluid flow under low ambient conditions. The product is used for freeze protection and process temperature maintenance systems such as product pipelines, process water, dust suppression systems, lube oil and condensate return.MI (Mineral Insulated) Cable
MI Cable is a metal sheathed cable that uses a metallic conductor as the heating element. It is custom designed and fabricated for specific applications. MI Cable is a high performance, industrial grade heat tracing cable used for applications requiring high temperature exposure, immunity to stress corrosion, high maintain temperature, under tank heating (cryogenic tanks), high power output, constant power output over entire, rugged cable construction heater length, and extended heater life.It is critical to consider the specific application requirements for any heat tracing application. The following checklist always needs to be clearly understood:
- The mass and material of the item being traced
- Insulation availability - type and thickness
- Temperature to be maintained
- Minimum ambient temperature
- Minimum start-up temperature
- Available supply voltage
- The chemical environment - expose
- Maximum intermittent exposure temperature
- Electrical area classification
White Paper: Breakthrough Solenoid Valve Technology for Upstream Oil and Gas Heating Equipment
within gas fuel trains in process heating system burners. These systems are widely used by oil and gas firms as well by as original equipment manufacturers (OEMs) that produce gas heating equipment or burner management systems (BMSs) and controls in upstream oil and gas pipelines and tanks.
In recent years, a new generation of solenoid valve technology has been changing the shutoff valve game. Their modern designs provide pipeline and tank heating systems with robust, durable performance; safety; and regulatory compliance — all while increasing efficiency and productivity.
Many operators in North America and beyond are moving away from using pneumatically operated shutoff valves on their pipelines and tank heaters. They’re replacing them instead with valves introduced within the last decade by a few manufacturers — all based on solenoid shutoff valve technologies. White paper courtesy of ASCO.
A Proven Ultrasonic Level Transmitter for Environmental, Water/Wastewater, and Energy Management Industries
![]() |
Reliable level control for environmental applications SITRANS LU150/180 |
Designed primarily for liquid applications in the environmental, water/wastewater, and energy management industries, the device is ideal for non-contact continuous level measurement of liquids and slurries in open or closed vessels.
The reliability of the level readings are based on Sonic Intelligence echo processing algorithms that Siemens has been refining for decades. These algorithms differentiate the true material level echoes from the false ones that can result from acoustic or electrical noises, as well as from agitator blades in motion. It's effective, accurate, unique, and it's exclusively Siemens.
Key Applications
- Chemical storage vessels
- Filter beds
- Mud pits
- Liquid storage vessels
- Food applications
Examining the User Interface of the SensAlert ASI Gas Detector
The product is third-party certified to IEC61508 Level 2 (SIL-2) for both hardware and software with certification to global hazardous area and performance standards. The Test-on-Demand feature with on-board gas generator provides remote functionality checks with generated gas while Predictive Sensor End-of-Life Indication provides advanced warning of impending sensor failure.
SensAlert ASI is a universal instrument platform for toxic & combustible gas detection and oxygen monitoring. Intrinsically safe or explosion proof installation configurations with options for remote sensors and gassing, duct mount, and sample-draw maximize application versatility. Intrinsically safe or explosion proof installation configurations for remote sensors and gassing, duct mount, and sample-draw maximize application versatility. The sensor head accepts all Plus Series sensor technologies – infrared, catalytic bead, and electro-chemical. Assignable and configurable relays together with communication options provide broad flexibility. The SensAlert ASI I.S. sensor head can be remote mounted up to 100 feet (30m) from the transmitter providing a useful option to position the transmitter in a personnel-accessible location while positioning the sensor closer to potential hazards.
Food Processing: Belt Scales Improve Tomato Processor Efficiency and Productivity
![]() |
Belt Scales Improve Tomato Processing |
Application:
A tomato processor located on the Pacific coast uses the latest technologies in peeling, dicing, and packaging tomatoes. They were preparing to replace some of their older weigh feeders because of declining performance. One of their main concerns with installing new weigh feeders was the cost of moving the existing conveying systems in order to accommodate new weigh feeders.
See the document below for the full case history:
2 Wire, 3 Wire, and 4 Wire RTD Sensor Connections
![]() |
Industrial temperature transmitters (courtesy of Siemens) |
![]() |
Proper wiring of RTDs |
For more information about any temperature measuring application, contact:
Ives Equipment
www.ivesequipment.com
(877) 768-1600
Combustion Analyzer Adds Higher Level of Safety by Measuring O2, Combustibles, and Methane

Low emission burners and aggressive firing control points to achieve increased efficiency and emission reductions have driven the industry to tighter control measures. But tighter control measures also hold a greater potential for combustion events. Reducing the risk of a combustion event has become a priority and has led to the implementation of Safety Instrumented Systems (SIS). This additional layer of safety is added to the Basic Process Control System.
The WDG-V has been designed to provide an additional layer of safety with the measurement of excess O2, Combustibles and Methane and by using these measurements to ensure the safe operation of the Burner Management System.
Lost Plant Air a Hidden Source for Energy Savings
![]() |
Save energy costs by reducing consumption of plant air. |
Plant maintenance are becoming more aware of air leaks and the subsequent increases in cost to overcome lost power because of those leaks. One of the major culprits for lost air in a plant is the pneumatic control valve positioner and the air required to operate them. In a typical process plant, there could be hundreds of control valves. Each control valve uses a positioner to move the valve actuator, based on a set point signal from a controller.
![]() |
Control valve with Siemens SIPART |
Years ago, when electricity was cheap and when valve positioners were first introduced, plant maintenance and engineering were not concerned with something called the “bleed rate” of the positioner. Over the years though, plant personnel lost track of bleed rate and pretty much forgot that a positioner is just part of the system and it operates on air. Today, a modern process facility such as a power plant, refinery, or chemical plant can have several hundred control valves with positioners. The combined air loss due to the positioner “bleed rate” can be significant.
![]() |
Siemens SIPART positioners |
The significant change in technology came with the adoption of the adoption of a piezo ceramic valve block in low bleed positioners. Traditional positioners used an I/P and spool valve which both leaked air. Over time the leaks from these two parts is significant.
Could you and your plant be in the situation where lost energy efficiency through leaky positioners is costing big bucks? If you’re even the slightest bit concerned, call in an applications expert now for a system review.
Compact Coriolis Flowmeter with NTEP Custody Transfer Approval
![]() |
NTEP approval for custody transfer |
When oil and gas are physically transferred from one operator to another, the term custody transfer is used to describe the transaction. It is understood as the transfer of fluid material defined by a metering device, at a given location, to another party. Custody transfer occurs at a variety of locations including from production platforms to ships, trucks, railcars, barges, and also at the final destination, such as the processing plant or refinery.
Accuracy is very important in custody transfer as both parties and instruments such as flowmeters must have approval by the organizations such as the American Petroleum Institute (API) or the National Conference on Weights and Measures (NCWM).
The National Type Evaluation Program (NTEP) is an evaluation program overseen by the National Conference on Weights and Measures (NCWM). Manufacturers who carry NTEP approval comply with local state and government regulations regarding transactions selling, purchasing, exchanging, custody transfer, or establishing the cost for services on based on weight.
![]() |
Compact Coriolis flowmeter with NTEP approval |
For more information, contact:
Ives Equipment
www.ivesequipment.com
877-768-1600
Upgrading a Mechanical Pressure Switch to an Electronic (Solid State) Version
The example here uses the United Electric Controls One Series as the example.
This type of product (One Series) allows you to choose from explosion-proof, intrinsically safe and energy limited models that monitor gauge pressure, differential pressure or temperature. With up to two fully adjustable set points and deadbands, available 4-20 mA analog output, and absolutely no moving parts. They are used in a wide variety of applications where mechanical switches are not considered.