Educational information on process control, industrial instrumentation, valves, valve automation and control valves. For additional information visit IvesEquipment.com or call 877-768-1600
Understanding HART Communication Protocol
A technological advance introduced in the late 1980’s was HART, an acronym standing for Highway Addressable Remote Transmitter. The purpose of the HART standard was to create a way for instruments to digitally communicate with one another over the same two wires used to convey a 4-20 mA analog instrument signal. In other words, HART is a hybrid communication standard, with one variable (channel) of information communicated by the analog value of a 4-20 mA DC signal, and another channel for digital communication whereby many other variables could be communicated using pulses of current to represent binary bit values of 0 and 1. Those digital current pulses are superimposed upon the analog DC current signal, such that the same two wires carry both analog and digital data simultaneously.
Looking at a standard loop-powered (2-wire) process transmitter circuit, we see the transmitter, a DC power supply (voltage source), and usually a 250 ohm resistor to create a 1 to 5 volt signal readable by any voltage-sensing indicator, controller, or recorder:
The transmitter’s primary function in this circuit is to regulate current to a value representative of the measured process variable (e.g. pressure, temperature, flow, etc.) using a range of 4 to 20 mA, while the DC voltage source provides power for the transmitter to operate. Loop-powered instruments are very common in industrial instrumentation because they allow both power and (analog) data to be conveyed on the same pair of wires.
With the advent of microprocessor-based process transmitters, it became possible for instrument technicians to digitally configure parameters inside the transmitter (e.g. range values, damping values) and also query the transmitter for self-diagnostic alarms. In order to make full use of this digital functionality, though, there had to be some way to communicate digital data to and from the process transmitter over the same two wires used to convey the 4-20 mA analog signal. Otherwise, the only way to access this rich array of digital data inside the transmitter would be to connect a communicator device to some data port located on the transmitter itself, which is inconvenient due to the nature of how these transmitters are used in industry (located in dirty places, often hard to access while carrying a personal computer or other communication device).
Thus the HART communication protocol was born to address this need. HART communicates digital data along the loop conductors in the form of AC signals (audio-frequency tones) superimposed on the 4-20 mA DC current signal. A modem built into the smart transmitter translates these AC signals into binary bits, and vice-versa. Now, instrument technicians could “talk” with the new microprocessor-based transmitters simply by connecting a HART communications device at any point along the two-wire cable, even at the far end where the cable terminates at the control system hardware (panel-mounted controller, PLC, DCS, etc.).
Being able to communicate digital data over the same wire pair as the DC power and analog signal opens a whole new range of possibilities. Now, the field-mounted transmitter can communicate self-diagnostic information, status reports, alarms, and even multiple process variables to the control system in addition to the original analog signal representing the (main) process variable. With digital communication, the only data limitation is speed (data rate), not quantity. The control system may even communicate information to the transmitter using the same digital protocol, using this digital data channel to switch between different measurement range sets, activating special features (e.g. square-root characterization, damping, etc.), automatically and remotely.
Reprinted from "Lessons In Industrial Instrumentation" by Tony R. Kuphaldt – under the terms and conditions of the Creative Commons Attribution 4.0 International Public License.
Looking at a standard loop-powered (2-wire) process transmitter circuit, we see the transmitter, a DC power supply (voltage source), and usually a 250 ohm resistor to create a 1 to 5 volt signal readable by any voltage-sensing indicator, controller, or recorder:
The transmitter’s primary function in this circuit is to regulate current to a value representative of the measured process variable (e.g. pressure, temperature, flow, etc.) using a range of 4 to 20 mA, while the DC voltage source provides power for the transmitter to operate. Loop-powered instruments are very common in industrial instrumentation because they allow both power and (analog) data to be conveyed on the same pair of wires.
With the advent of microprocessor-based process transmitters, it became possible for instrument technicians to digitally configure parameters inside the transmitter (e.g. range values, damping values) and also query the transmitter for self-diagnostic alarms. In order to make full use of this digital functionality, though, there had to be some way to communicate digital data to and from the process transmitter over the same two wires used to convey the 4-20 mA analog signal. Otherwise, the only way to access this rich array of digital data inside the transmitter would be to connect a communicator device to some data port located on the transmitter itself, which is inconvenient due to the nature of how these transmitters are used in industry (located in dirty places, often hard to access while carrying a personal computer or other communication device).
![]() |
HART Transmitter (Siemens) |
Thus the HART communication protocol was born to address this need. HART communicates digital data along the loop conductors in the form of AC signals (audio-frequency tones) superimposed on the 4-20 mA DC current signal. A modem built into the smart transmitter translates these AC signals into binary bits, and vice-versa. Now, instrument technicians could “talk” with the new microprocessor-based transmitters simply by connecting a HART communications device at any point along the two-wire cable, even at the far end where the cable terminates at the control system hardware (panel-mounted controller, PLC, DCS, etc.).
Being able to communicate digital data over the same wire pair as the DC power and analog signal opens a whole new range of possibilities. Now, the field-mounted transmitter can communicate self-diagnostic information, status reports, alarms, and even multiple process variables to the control system in addition to the original analog signal representing the (main) process variable. With digital communication, the only data limitation is speed (data rate), not quantity. The control system may even communicate information to the transmitter using the same digital protocol, using this digital data channel to switch between different measurement range sets, activating special features (e.g. square-root characterization, damping, etc.), automatically and remotely.
Reprinted from "Lessons In Industrial Instrumentation" by Tony R. Kuphaldt – under the terms and conditions of the Creative Commons Attribution 4.0 International Public License.
Labels:
communications,
Delaware,
HART,
instrumentation,
Maryland,
New Jersey,
New York,
Pennsylvania,
Process Control,
Virginia
New 2018 United Electric Controls Short Form Product Catalog
United Electric Controls is a premier manufacturer of safety, alarm, and shutdown equipment, and is a a global supplier of pressure and temperature switches, transmitters, sensors, and controls for the process, discrete, semiconductor, aerospace, and defense industries.
The UEC short form product catalog has been updated and can be downloaded here.
The UEC short form product catalog has been updated and can be downloaded here.
Labels:
Delaware,
Maryland,
New Jersey,
New York,
Pennsylvania,
pressure switches,
safety,
SIL,
temperature switches,
transmitters,
Virginia
US Navy Supplier of MIL-SPEC Valves, Instrumentation, and Analyzers
Ives Equipment is an authorized US Navy supplier for ASCO, Worcester Valve, Niagara Meter (Venture Measurement), Siemens, and REOTEMP , registered under Cage Codes 1H855 and 6F024.
https://ivesequipment.com/navy
(877) 768-1600
https://ivesequipment.com/navy
(877) 768-1600
Labels:
analyzers,
ASCO,
instrumentation,
Niagara,
Reotemp,
Siemens,
United States Navy,
US Naval Supplier,
US Navy,
Valves,
Worcester
The Samson 3291 and 3255 Series Control Valves
Samson Controls, located in Baytown, TX, manufactures high-performance, industrial control valves designed to withstand the toughest applications.
The Samson 3291 control valve was specifically developed for heavy duty applications in the oil and gas industry. The construction is based on the proven SAMSON valve design, with one significant difference: while the seats in SAMSON valves are normally screwed in place, the 3291 has the seat held in place by a cage retainer. Unlike typical cage guided control valves, the 3291 control valve utilizes a top and seat guided design by means of a V-port plug. This open flow-path design minimizes friction and allows for the passage of small particulates without clogging the valve or getting “trapped” between the piston and cage. To download the Samson 3291 Control Valve brochure visit this page.
The Samson 3291 Special Length Version is a direct replacement for legacy split body valves without the need for spool pieces, piping modifications, or on-site modifications.
Samson 3291
![]() |
Samson 3291 |
The Samson 3291 Special Length Version is a direct replacement for legacy split body valves without the need for spool pieces, piping modifications, or on-site modifications.
![]() |
Samson 3522 "Little Tex" |
Samson 3522 "Little Tex"
The Type 3522 threaded seat control valve is designed for standard process engineering applications with high industrial requirements for control and quality. This control valve offers a wide range of trim sets to meet required flow coefficient and sealing methods as would be found in general application type control valves. The Type 3522 can be assembled with a pneumatic, electric, hydraulic, or electro-hydraulic actuator also offered by the SAMSON group to complete the control valve construction. To download the Samson 3522 Control Valve brochure visit this page.
Labels:
3291,
3522,
control valve,
Delaware,
Little Tex,
Maryland,
New Jersey,
New York,
Pennsylvania,
Samson,
Virginia
New Flowserve Worcester Controls Industrial Valve and Actuator Catalog
The latest catalog for Flowserve Worcester Control industrial ball valves, pneumatic actuators and electric actuators, courtesy of Ives Equipment. Worcester was founded in 1955. It supplies valves throughout the world for virtually any application. These include standard flanged ball valves, ANSI and DIN specifications in reduced and full bore, three-piece valves for cryogenic, high pressure, steam, diverter or sampling duty, high integrity valves, multi-way designs, modulating controls or customized solutions.
Download a PDF version of the "Worcester Controls Industrial Valve and Actuator Catalog" here or review in the embedded document below.
Download a PDF version of the "Worcester Controls Industrial Valve and Actuator Catalog" here or review in the embedded document below.
Labels:
actuator,
ball valve,
cryogenic valve,
Delaware,
Flowserve,
Maryland,
Navy Valves,
New Jersey,
New York,
Pennsylvania,
Virginia,
Worcester
Positive Displacement Flowmeters
![]() |
Oval Gear Flowmeter (Macnaught) |
- Oscillating piston
- Oval Gear
- Nutating disk
- Rotary vane
- Diaphragm
![]() |
Oscillating Piston Flowmeter (Niagara Meter) |
Positive displacement flowmeters can be applied to liquid or gaseous media, with the selection of the mechanical internals being a significant factor in the suitability of a design for a particular application. The longstanding use of positive displacement flowmeters across various industries has been a source of stability in terms of design, with the most recent advancements in positive displacement technology focusing on maintaining precision at lower costs.
![]() |
Nutating Disc Flowmeter (Niagara Meter) |
There are a few known limitations for the use of positive displacement meters. The meters are not the optimal choice for measuring fluids with large particles, and are also non-ideal for measuring fluids with large air pockets. Additionally, systems using positive displacement meters need to account for slight pressure drops in the positive displacement meter.
Share all of your flow measurement requirements and challenges with process instrumentation experts, combining your own process knowledge and experience with their product application expertise to develop effective solutions.
Understanding Valve Positioners
![]() |
Valve positioner on linear control valve (Siemens SIPART) |
A valve positioner is used in tandem with a valve actuator, the power source to open or close the valve. Positioners precisely direct the actuator to move the valve so that a desired flow volume is achieved and maintained. The positioner does this by monitoring the process condition, comparing it to a desired set point, and then pneumatically, electrically, or hydraulically manipulating the valve orifice until the difference between the set point and actual process variable is zero.
In closed loop control systems where the final control element are valves, valve positioners are the "brains" that provide the corrective signal to eliminate process offset. Positioners enable tighter control by overcoming the realities of valve wear, imprecise calibration, and a host of other process variable challenges.
Valve positioners are used throughout the process industries including power, pharmaceutical, chemicals, oil and gas, food and beverage, pulp and paper, refining and petrochemicals, pipelines, and many other processes.
Basic Function
![]() |
Diagram of typical flow control loop using valve positioner. |
Types of valve positioners:
Pneumatic Positioners
Pneumatic positioners receive pneumatic signals (3-15 or 6-30 PSIG) and proportion the supply air pressure to the valve actuator accordingly to move the valve to the required position. Pneumatic positioners are intrinsically safe and have the ability to provide a large amount of force to open or close a valve.Electro-Pneumatic Positioners
Electro-pneumatic valve positioners are very similar to pneumatic postioners, except that they contain internal current-to-pneumatic converter (I/P). The current-to-pneumatic module receives a varying electrical signal (most commonly 4-20 mA) and converts that signal (proportionately) to a pneumatic output signal (3-15 PSIG or 6-30 PSIG). The pneumatic signal then then proportions the supply air pressure to the valve actuator.Electric Positioners
Electric valve positioners receive an electric signal, usually 4-20 mA, 1-5 VDC, 2-10 VCD or 0-10 VDC and generally drive the motors in electric actuators. They perform the same function as pneumatic positioners do, but use electricity instead of air pressure as an input signal.For more information on valve positioners, or any valve automation requirement, contact Ives Equipment by visiting https://ivesequipment.com or calling 877-768-1600.
Labels:
Delaware,
Maryland,
New Jersey,
New York,
Pennsylvania,
positioner,
Siemens,
SIPART,
valve automation,
Virginia
Tutorial: How to Use the Push Buttons on the SIEMENS SITRANS P Family of Transmitters
The SIEMENS SITRANS P stands above the competition when it comes to easy operation. This video provides an outstanding tutorial on how the SITRANS P push buttons and display are used.
SITRANS P offer a complete family of devices that include digital pressure transmitters for measuring gauge pressure, absolute pressure, differential pressure, flow and level.
https://ivesequipment.com
(877) 768-1600
SITRANS P offer a complete family of devices that include digital pressure transmitters for measuring gauge pressure, absolute pressure, differential pressure, flow and level.
https://ivesequipment.com
(877) 768-1600
Labels:
Delaware,
Maryland,
New Jersey,
New York,
Pennsylvania,
Siemens,
Sitrans P,
transmitter,
tutorial,
Virginia
Excellent Reference for Engineers: Table of Gases
![]() |
Handy Table of Gases courtesy of Control Instruments |
The table can be found here: http://www.controlinstruments.com/table-of-gases
Control Instrument Corporation manufacturers gas detection instruments for safety and environmental protection. Control Instruments products are installed and used under the most demanding conditions, from oil pipelines in the Arctic to drilling wells in the desert.
Control Instrument Corporation manufacturers gas detection instruments for safety and environmental protection. Control Instruments products are installed and used under the most demanding conditions, from oil pipelines in the Arctic to drilling wells in the desert.
For more information on Control Instruments products, contact Ives Equipment by visiting https://ivesequipment.com, or by calling (877) 768-1600.
What Are Rack and Pinion Actuators?
![]() |
Operation rack and pinion actuator. |
There are three primary kinds of valve actuators are commonly used: pneumatic, hydraulic, and electric.
Pneumatic actuators can be further categorized as scotch yoke design, vane design, and the subject of this post - rack and pinion actuators.
How Rack and Pion Actuators Operate
![]() |
Image courtesy of Wikipedia |
Pneumatic actuators use pistons that are attached to the rack. As air or spring power is applied the to pistons, the rack changes position. This linear movement is transferred to the rotary pinion gear (in both directions) providing bi-directional rotation to open and close the connected valve.
Rack and pinion actuators pistons can be pressurized with air, gas, or oil to provide the linear the movement that drives the pinion gear. To rotate the pinion gear in the opposite direction, the air, gas, or oil must be redirected to the other side of the pistons, or use coil springs as the energy source for rotation. Rack and pinion actuators using springs are referred to as "spring-return actuators". Actuators that rely on opposite side pressurization of the rack are referred to as "direct acting".
![]() |
Internal view of rack and pinion actuator |
NAMUR mounting dimensions on actuator pneumatic port connections and on actuator accessory holes and drive shaft are also common design features to make adding pilot valves and accessories more convenient.
![]() |
Rack and pinion actuator with valve. (Flowserve Worcester) |
Share your process valve control and automation challenges with application experts, and combine your process experience and knowledge with their product application expertise to develop effective solutions.
Labels:
Delaware,
Flowserve,
Maryland,
New Jersey,
New York,
Pennsylvania,
rack and pinion,
valve actuation,
Virginia,
Worcester
Macnaught Now Offers Explosion Proof/Flame Proof (Ex D) Sensors for Hazardous Areas on MX-Series
![]() |
Macnaught MX Series |
Macnaught is proud to now extend its range of pulse output options to include Ex D flame proof approved sensors for hazardous areas.
Download the MX-Series Explosion Proof/Flame Proof (Ex D) Sensors for Hazardous Areas cut sheet here, or review the embedded document below. For more information on Macnaught flowmeters, contact Ives Equipment by visiting https://ivesequipment.com or call (877) 768-1600.
Alfa Laval UltraPure Pumps: LKH UltraPure, LKH Prime UltraPure, SolidC UltraPure, SX UltraPure
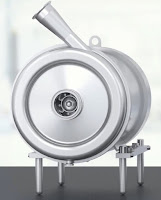
LKH UltraPure
Designed to meet the specific demands of the biotech and pharmaceutical industries, LKH UltraPure centrifugal pumps deliver maximum uptime and high efficiency plus the benefits of easy cleanability.LKH Prime UltraPure
The LKH Prime UltraPure is an efficient, versatile self-priming pump designed for Cleaning-in-Place duties containing entrained air with the ability to also pump product in pharmaceutical industry.SolidC UltraPure
The special features of SolidC UltraPure centrifugal pumps include an external shaft seal and spring, a defined-compression O-ring on the back plate and crevice-free design.SX UltraPure
Alfa Laval’s premium rotary lobe pump designed for gentle transportation of process fluids in high purity applications in the biotechnology and pharmaceutical industries.https://iveequipment.com
(877) 768-1600
Labels:
Alfa Laval,
Biotech,
Delaware,
hygienic,
Maryland,
New Jersey,
New York,
Pennsylvania,
pharmaceutical,
pumps,
sanitary,
Virginia
Five Key Reasons You Should Consider Oval Gear Flow Meters
Oval gear flow meters are simple and robust. They operate by interlocking two oval gears, offset by 90 degrees, inside the meter housing which are then rotated by the flowing media. They are very rugged and designed to operate in very harsh environments. Accuracy is maintained irrespective of temperature, viscosity change, or flow pulsation. It's not unusual to see these meters perform in the field for 30 to 40 years.
Five Reason You Should Consider Oval Gear Flow Meters
![]() |
Internal view of oval gear flow meter (Macnaught) |
- No flow conditioning - put the meter where you want it. Locate off pumps, valves, U bends with no loss in accuracy or repeatability.
- Compact meter footprint allows for excellent OEM or MRO install challenge solutions
- Accuracy is unaffected by viscosity changes.
- Heavy Duty - meter construction is designed for vibration, dust, piping hammer, low & high ambient temperature conditions -40F to 302F.
- Outstanding flow turndown gives best cost of ownership meter sizing potential.
For more information on oval gear flow meters, contact Ives Equipment by visiting https://ivesequipment.com or calling (877) 768-1600.
Valves and Automation for Hygienic, High Purity, or Sanitary Use
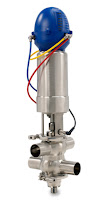
You can review the embedded document below, or download your own PDF version of Alfa Laval Valves and Automation for Hygienic here.
Basics of Thermocouple Junction Design
![]() |
Industrial thermocouples (AST) |
A thermocouple has three variations of sensing tip (or junction):
- Exposed junction, where the exposed wire tips and welded bead have no covering or protection.
- Grounded junction, where the welded bead is in physical contact with the thermocouple's sheath.
- Ungrounded junction, where the tip is inside the thermocouple sheath, but is electrical (and somewhat thermally) insulated from the sheath (no sheath contact).
Exposed junction thermocouples respond to temperature change quickly and are less costly, but their signals are susceptible erratic reading caused by induced or conducted electrical noise. Because there is no sheath, they are also prone to mechanical damage and ambient contamination.
Grounded junction thermocouples provide fast response and are mechanically more robust, with a metallic sheath that protects the thermocouple both mechanically and from contaminants. But because their sensing tip is in contact with the external sheath, their signal still can be affected by externally induced or conducted electrical noise.
Ungrounded thermocouples, like grounded, are protected mechanically and from ambient contaminants by their sheath. However, their sensing junctions are kept separate from their metallic sheath, isolating the junction from external electrical interference. This separation does come at a small cost in temperature sensing responsiveness though.
For safety, precision, and optimum performance, always talk to an applications specialist when applying temperature sensors. A short phone call can prevent major headaches and lost time in troubleshooting a misapplied thermocouple.
Ives Equipment: Growth and Leadership in Automation and Control
For over 60 years, Ives Equipment Corporation has successfully served the industries of eastern and central Pennsylvania, Delaware, Maryland, New Jersey, metro NY, and Virginia with the latest in process control equipment and services. Our business has been built on a foundation of quality people, highly trained and experienced, who take a keen interest in finding the optimum solutions to our customers' control problems.
Accurate Low-Flow Measurement and High-speed Communication in Supercritical Fluid Extraction and Chromatography Systems
![]() |
Low-Flow Measurement in Supercritical Fluid Extraction |
A food producer removes caffeine from coffee beans to create a decaffeinated version of its most popular blend. A manufacturer of dietary supplements extracts pesticides and organic solvents from ginseng to ensure a higher-quality end product. A crime laboratory measures the amount of morphine in a blood sample to analyze the usage habits of a drug addict.
These scenarios might not appear to share much in common – after all, what does your favorite morning beverage have to do with forensic drug testing? – but there are important similarities. In each example, a supercritical fluid can be used to carry out precise, efficient, low-toxicity chemical extraction or chromatography.
![]() |
SITRANS F C MASS 2100 sensor paired with the SITRANS FCT010 digital transmitter |
Download this Application Note Here
The Application
An analytical science corporation in the northeastern USA develops instruments for laboratory-based applications across a broad range of industrial, academic and government organizations. Among their specialties are SFE and SFC systems tailored to the specific needs of customers and designed to extract and/or measure a variety of chemical compounds.
Their systems rely on supercritical carbon dioxide (CO2) instead of organic solvents to provide selective sample extractions and/or measurement. CO2 normally behaves as a gas at standard temperature and pressure, or as dry ice when frozen. But when CO2 is held at or above its critical temperature of 31.2 °C (87.8 °F) and critical pressure of 73.8 bar (1071.6 psi), it achieves a super- critical state midway between a gas and a liquid, with liquid-like density and solvating power but a viscosity near zero. Using supercritical CO2 results in shorter completion times and purer extracts – not to mention lower operating costs in comparison to solvent-based systems.
To kick off SFE or SFC, supercritical CO2 is pumped into the system and passes through an integrated Coriolis flowmeter, which measures the incoming mass flow rate, density and temperature. This is a crucial step in both processes, as it’s the prima- ry way to ensure that all CO2 flowing into the system remains in the desired fluid state. Once conditions are verified by the flowmeter, the CO2 helps to extract the compounds (in SFE) or separate and measure them (in SFC).
The Challenge
For more than 15 years, the company has had the option to add a SITRANS F C Coriolis flowmeter from Siemens to their SFE and SFC systems, depending on customer requirements. Their meter of choice consisted of a MASS 2100 sensor in size DI 1.5 (1/16”) and a MASS 6000 transmitter. They initially selected the Siemens solution because of its capability for very accurate measurement – as high as 0.1% of flow rate – under the low-flow conditions required for chemical extraction and measurement with supercritical CO2. The robust construction of the MASS 2100 sensor also offered the reassurance of long-term durability, even in high-pressure environments.
Over time, the company recognized the need to expand into a broader market- place by ensuring that all of their super- critical fluid solutions complied with the RoHS Directive for hazardous materials, which would open the opportunity to sell into the European Union. Having come to appreciate the reliability of the SITRANS F C product line and the responsiveness of Siemens customer support, they turned to Siemens for a digitally based, RoHS-compliant Coriolis flow alternative. That’s when they were introduced to the SITRANS FCT010.
The Solution
Part of the next-generation digital flow platform from Siemens, the FCT010 is a powerful, very compact Coriolis transmitter designed especially for skids and other small-footprint assemblies – a major benefit for the SFE and SFC systems given their limited availability of space.
Another prerequisite for selection was superior performance, and the FCT010 does not disappoint. The transmitter measures with advanced digital signal processing technology, so it produces a stronger signal-to-noise ratio than an analog transmitter for higher accuracy, improved resistance to process noise and a more stable zero point. The FCT010 can also detect and respond to even the smallest changes in flow with a best-in-class 100 Hz update rate.
The company was pleased to learn that the new transmitter could be paired seamlessly with the existing MASS 2100 sensor, which over the course of 15 years has proven to be the ideal low-flow sensor for measuring supercritical CO2. They also liked that the FCT010 is extremely simple to install as a result of its small size and easy-to-use wiring connections.
Ultimately, they placed an order for 100 FCT010 transmitters to be included with new SFE and SFC systems. Now that the enhanced Coriolis flow solutions are in place, the upgraded systems are benefit- ting from faster communication coupled with better process data – all of which adds up to higher-precision, more effi- cient extractions and measurements for laboratories.
With help from the digitally powered SITRANS F C Coriolis flow family, the corporation is equipping manufacturers and researchers with advanced tools that optimize science, commerce and their bottom lines.
For more information, call Ives Equipment at (877) 768-1600 or visit https://ivesequipment.com.
Expertly Applying Process Control Instrumentation, Valves, and Process Equipment for Over 60 Years
Ives Equipment, founded in 1954, provides a diverse range of process control equipment, including valves, regulators, wireless products, flow products, pressure gauges, control products, level instrumentation, sanitary products, temperature instruments, analytical products, electric heat trace and bio-pharmaceutical products.
Explosion-Proof ASIC or HART Pressure Transmitter
![]() |
UE TX200 |
The fixed range model TX200B is recommended for use where process pressure is consistent within the range and where physical access to the transmitter is limited or not required.
The field adjustable model TX200A allows access to zero and span the transmitter. The transmitter may be spanned up to 5:1 and for ease of calibration, does not require a calibrated pressure source and can be calibrated in-place.
Both TX200 models feature an all welded, 316 stainless steel hermetically sealed enclosure providing airtight and watertight protection within the harshest environments. A 316 stainless steel, rotatable cover protects product markings and adjustment buttons (TX200A) from the elements and tampering. The TX200 lends itself to control panel mounting or direct process mounting due to its light-weight, cylindrical design.
TX200H Hart Models
The TX200H is a HART Smart pressure transmitter that provides simplified eld adjustment while reliably communicating asset management data utilizing the latest HART 7 specification. A proprietary calibration process insures optimum temperature compensation limiting thermal effects on the sensor output. As with the ASIC TX200, it is suited for process control industries worldwide and provides a cost-effective solution to using conventional HART transmitters.
Download the PDF cut sheet for the UE TX200 from this link or read the embedded document below.
For more information on United Electric Controls products, contact Ives Equipment by calling (877) 768-1600 or by visiting https://ivesequipment.com.
What Are Turbine Flow Meters?
![]() |
Turbine Flow Meter (Niagara WPX) |
Turbine flow meters use the mechanical energy of the fluid to rotate a turbine blade in the flow stream and provide precise and accurate flow measurement. The flow impinging upon the turbine blades causes the rotor to spin. The angular velocity of a turbine flow meter is proportional to flow rate. The rotational velocity of the turbine is interpreted as an electrical frequency output through the use of magnetic pick-ups. As each turbine blade passes by the magnetic pick-up coil, a voltage pulse is generated which is a measure of the flow rate. The total number of pulses gives a measure of the total flow which can be totalized with a maximum error of a single pulse.
The relationship of the angle of the turbine meter blades to the flow stream governs the angular velocity and the output frequency of the meter. The sharper the angle of the turbine blade, the higher the frequency output.
Easy to maintain while also boasting reliability, turbine flow meters are known to be cost-effective solutions that make an ideal device for measuring flow rate. Aside from excellent rangeability, they also provide high response rate and high accuracy compared to other available types of flow meters. Turbine flow meters are sturdy, need very little maintenance, and seldom exhibit much deviation in performance.
These meters are used in multiple industries to reliably measure the velocity of a variety of liquids, gases and vapors over a very broad range of flow rates, temperatures, and viscosities. Turbine flow meters are used to provide measurement information in crude oil production, chemical processing, blending systems, tank storage, product off-loading, product loading, and many other applications across many industries.
Advantages
- Simple and durable structure
- Easy to install and maintain
- Low pressure drop
- Operate best in applications with fast, steadyflows
- Operate under a wide range of temperatures and pressures
- Require straight run of pipe upstream and downstream
- Need constant back-pressure
- Best for lower fluid viscosity
- Bubbles in liquids affect accuracy
- Bearing wear
(877) 768-1600
Labels:
Delaware,
flow control,
Maryland,
New Jersey,
New York,
Niagara,
Pennsylvania,
Turbine flow meters,
Virginia
An Exceptional Clamp- on Ultrasonic Flow Measurement Solution for Any Liquid Process
The SITRANS FS230 digital clamp-on ultrasonic flowmeter is a process-optimizing solution for measuring flow in virtually any liquid application. Designed to provide both exceptional performance and outstanding cost savings, the FS230 is an ideal fit for many industries requiring high-quality liquid flow measurement – including water and wastewater, HVAC and power, food and beverage, pharmaceutical, chemical, mining and pulp and paper.
The SITRANS FS230 flow system consists of a SITRANS FST030 transmitter paired with SITRANS FSS200 clamp-on ultrasonic sensors, which are available in three different models: WideBeam® (High-Precision), Universal and High-Temperature.
Download the PDF from the Ives Equipment web site here, or read the document embedded below.
For more information, contact Ives by calling 877-768-1600 or by visiting https://ivesequipment.com.
The SITRANS FS230 flow system consists of a SITRANS FST030 transmitter paired with SITRANS FSS200 clamp-on ultrasonic sensors, which are available in three different models: WideBeam® (High-Precision), Universal and High-Temperature.
Download the PDF from the Ives Equipment web site here, or read the document embedded below.
For more information, contact Ives by calling 877-768-1600 or by visiting https://ivesequipment.com.
Labels:
Clamp On,
Delaware,
flow meter,
Maryland,
New Jersey,
New York,
Pennsylvania,
Siemens,
SITRANS FS230,
Ultrasonic,
Virginia
SIEMENS SITRANS LR250
The SIEMENS SITRANS LR250 is a great choice for liquid level measurement in storage and process vessels up to 66 feet (20 meters). With a variety of antennas, the LR250 can handle a broad scope of level applications. The SITRANS LR250 flanged and hygienic encapsulated antennas mean corrosive or aggressive materials and hygienic or sanitary requirements are no challenge for this transmitter.
https://ivesequipment.com
877-768-1600
https://ivesequipment.com
877-768-1600
Siemens SIWAREX WT231 and WT241 Weighing Terminals

SIWAREX is the optimum solution wherever strain gauge sensors, such as load cells, force sensors or torque measuring shafts, are used for measuring tasks. The typical applications of SIWAREX are:
- Non-automatic scales
- Fill level monitoring of silos and bunkers
- Measuring of crane and cable loads
- Load measuring for industrial lifts and rolling mills
- Force measuring, container weighers, platform scales and crane scales
- Complete solution – no configuration in SIMATIC required
- Fast and easy commissioning due to intuitive operating concept
- The stainless steel enclosure permits applications in many diverse environments
- Integrated connecting terminals for up to 4 load cells
- Flexible connection to different systems through diverse interfaces
- - four digital inputs
- - four digital outputs
- - one analog output
- - RS 485 interface and Modbus RTU
- High resolution of the load cell signal of up to ± 4 million parts
- Comprehensive diagnostics functions
- Recovery-point for the simple restoration of all parameters
- Automatic calibration is possible without the need for calibration weights
- All diagnostic and error messages as well as all scale parameters in plain text
- 100-240 VAC supply range
Contact Ives Equipment by calling 877-768-1600 of by visiting https://ivesequipment.com.
Electronic Pressure Measurement: AMETEK USG Model 1536 Stainless Steel Semiconductor Pressure Gauges
Download the PDF here.
DESCRIPTION
DESCRIPTION
![]() |
AMETEK USG Model 1536 Stainless Steel Pressure Gauge for Semiconductor Industry |
AMETEK U.S. Gauge Model 1536 pressure gauges are designed and manufactured for gas distribution equipment used in semiconductor manufacturing. These 2 inch, all stain- less steel gauges are clean room produced, nitrogen purged, and double bagged.
These instruments are compatible with many toxic and corrosive gases. Welded face seal connections provide a threadless pressure seal and virtually eliminate a major source of contamination. Also available in NPT connections.
The Model 1536 is available in pressure ranges from 0 to 30 inches Hg VAC, to 0 to 4000 psi. This precision gauge incorporates rugged case construction with pressure relief.
FEATURES
These instruments are compatible with many toxic and corrosive gases. Welded face seal connections provide a threadless pressure seal and virtually eliminate a major source of contamination. Also available in NPT connections.
The Model 1536 is available in pressure ranges from 0 to 30 inches Hg VAC, to 0 to 4000 psi. This precision gauge incorporates rugged case construction with pressure relief.
FEATURES
- Cleaning for UHP gas applications exceeding ANSI B40.100 specifications
- Ra: 10 μinch (0.25 μm) finish on face seal connections
- Helium leak tested to con rm leakage rates of less than 10-9 scc/sec.
- All stainless steel (Type 316L) internal surfaces for corrosion resistance
- Large, easy-to-read dial graduations
- Handles wide variety of exotic gases
- Available with welded face seal fittings, or NPT connection
- Assembled and packaged in Class 10 clean room
- Low mount or center back connections
SPECIFICATIONS
![]() |
Close-up of VCR connection |
- Size: 2 inch diameter
- Case: Drawn stainless steel polished with pressure relief Ring and Window: One piece, threaded polycarbonate Pointer: Aluminum, black finish.
- Dial: Aluminum, white background with black markings Bourdon Tube: Type 316L stainless steel.
- Connection: Type 316L stainless steel, low mount or center back mount, male or female face seal fitting, or 1/4 inch male NPT – connectors are shipped with protective plastic caps.
- Surface Finish:
- Face seal connections: Ra: 10 μinch (0.25 μm) 1/4 inch NPT connections: 32 Ra.
- Ranges: 30 inches Hg vacuum to 4000 psi, single or dual scale, see ordering information.
- Overpressure: 130% of span maximum Working Temperature:
- Ambient: -40°F (-40°C) to 149°F (65°C) Fluid: Maximum 212°F (100°C) Accuracy:
- ±1% of span.
- Scales: psi, bar, kg/cm2, KPa, MPa (single or dual scale) inches Hg (for vacuum range, compound and vacuum gauges only).
Labels:
Delaware,
gauge,
Maryland,
measurement,
New Jersey,
New York,
Pennsylvania,
pressure,
semiconductor,
Virginia
What Are Industrial Control Systems?
![]() |
Control system diagram (click for larger view). |
In certain industries such as chemical and power generation, safety systems are typically implemented to mitigate a disastrous event if control and other systems fail. In addition, to guard against both physical attack and system failure, organizations may establish back-up control centers that include uninterruptible power supplies and backup generators.
There are two primary types of control systems. Distributed Control Systems (DCS) typically are used within a single processing or generating plant or over a small geographic area. Supervisory Control and Data Acquisition (SCADA) systems typically are used for large, geographically dispersed distribution operations. A utility company may use a DCS to generate power and a SCADA system to distribute it.

Contact Ives Equipment with any control systems question of challenge. Reach them by calling (877) 768-1600 or by visiting https://ivesequipment.com.
Alfa Laval Hygienic Liquid/Liquid Gasketed Plate and Frame Heat Exchanger
The following video illustrates the working principle of an Alfa Laval liquid/liquid 1-pass gasketed plate-and frame heat exchanger for use in hygienic applications. The hot liquid (shown in red) typically enters through one of the top connections and leaves through a lower connection. The cold liquid (shown in blue) enters through one of the bottom connections and leaves through the connection on top. Heat is transferred from the hot media to the cold media as the fluids pass through the heat exchanger.
The fluids enter the heat transfer plates through the connections and portholes. Highly engineered sealing gaskets between the plates direct the fluids so that the hot and cold fluids pass counter-currently in alternating channels. When the fluid enters between the plates, it passes over the distribution area. Alfa Laval’s unique design distribution area is one of the most important features of a plate heat exchanger as it ensures an even flow of fluid over the entire plate, maximizes heat transfer efficiency, and minimizes maldistribution and fouling.
Note in the video the distribution area helps the fluids quickly fill up the entire cross section of the plates.
For very heat sensitive media, co-current flow is used in gasketed plate-and-frame heat exchangers allowing the coldest fluid meets the hottest fluid when entering the heat exchanger. This minimizes the risk of overheating or freezing sensitive media. Watching the video, imagine that the hot fluid is reversed, so that both fluids are entering at the bottom connections.
Alfa Laval has an extremely broad range of gasketed plate-and-frame heat exchangers which are used in all types of industries.
For more information about heat exchanger for use in hygienic applications contact Ives Equipment by calling (877) 768-1600 or by visiting https://www.ivesequipment.com.
The fluids enter the heat transfer plates through the connections and portholes. Highly engineered sealing gaskets between the plates direct the fluids so that the hot and cold fluids pass counter-currently in alternating channels. When the fluid enters between the plates, it passes over the distribution area. Alfa Laval’s unique design distribution area is one of the most important features of a plate heat exchanger as it ensures an even flow of fluid over the entire plate, maximizes heat transfer efficiency, and minimizes maldistribution and fouling.
Note in the video the distribution area helps the fluids quickly fill up the entire cross section of the plates.
For very heat sensitive media, co-current flow is used in gasketed plate-and-frame heat exchangers allowing the coldest fluid meets the hottest fluid when entering the heat exchanger. This minimizes the risk of overheating or freezing sensitive media. Watching the video, imagine that the hot fluid is reversed, so that both fluids are entering at the bottom connections.
Alfa Laval has an extremely broad range of gasketed plate-and-frame heat exchangers which are used in all types of industries.
For more information about heat exchanger for use in hygienic applications contact Ives Equipment by calling (877) 768-1600 or by visiting https://www.ivesequipment.com.
Labels:
Alfa Laval,
Delaware,
Heat exchanger,
hygienic,
Maryland,
New Jersey,
New York,
Pennsylvania
Basic Information for the Design and Selection of Heat Trace Products for Pipe and Vessel Heating
![]() |
Heat Tracing Self-Regulating Cable |
To specify components for an effectively designed, totally electric heat trace system, it is necessary to understand the basic principles involved. A heat trace system is designed to replace heat lost through the thermal insulation from equipment in the system. In some applications, heat tracing will also be able to provide enough heat to significantly change the process temperature.
It is always recommended to use thermal insulation since heat loss from bare surfaces is very high and heat transfer between the heater and the pipe/vessel is highly variable. All insulation should be weatherproofed. Wet insulation is ineffectual and heater output is insufficient to dry it.
Self Regulating Heater Cable
Self Regulating Heater Cable will adjust its own output in response to pipe temperature. Available in a variety of temperature and power ratings up to 230°C (450°F) and 65.6w/m (20w/ft.). Product features include:
- Variable Output
- Self-Regulating heaters will react to variations in temperature encountered at every point along its length. Colder sections receive more heat output, while warmer sections receive less. This provides greater energy efficiency and more uniform pipe temperatures.
- Can Be Overlapped Without Damage
- Because Self-Regulating heaters controls its own output, overlapped sections produce less heat, eliminating “hot spots” and possible burn-through common with other types of cable.
- Fail Safe
- Upon reaching the upper limits of its temperature range, Self-Regulating heaters diminishes its own heat output to an insignificant level. This guarantees that maximum temperatures (T ratings) cannot be exceeded no matter what product is used in any application.
- Easy Installation
- Because of its infinite parallel path circuitry, Self-Regulating heaters can be cut to any length in the field without affecting the heat output or creating “dead zones”.
![]() |
Constant Wattage Heat Tracing Cable |
Constant Wattage Heater Cable is a parallel resistance heater that produces the same watts-per-foot of heat along its entire length.
- EasyInstallation
- Constant-Wattage heaters can be cut to length and terminated in the field.
- Economical
- Provides good power densities and exposure temperatures with parallel circuit cable capabilities at economical prices. Exposure Temperatures to +204°C (+400°F). Ideal for maintaining many process temperature applications.
![]() |
MI Cable |
Mineral insulated Cable is a series conductor, high temperature heater cable with a special, thin metal sheath. Some of MI advantages are:
- Corrosion-Resistant
- Alloy 825 sheath provides excellent corrosion resistance and immunity from chloride stress corrosion - a common problem with stainless steel.
- Ideal for High Temperature Applications
- Mineral Insulated heaters can withstand exposure temperatures up to 593°C (1100°F). Exposure temperatures can be increased to 750°C (1400°F) with special components.
- Ratings To 600V
- Mineral Insulated heaters are available in a variety of voltages to match the available power supply.
- High Heat Output
- Mineral Insulated heaters have heat output ratings up to 10 times higher than most other cables, reducing the amount of cable required.
- Rugged Construction
- A durable metal sheath provides greater mechanical protection.
- Thin Wall Construction
- A unique manufacturing process allows thin wall cable construction for easier field installation.
Tank Heating Panels
![]() |
Heating Panel |
- Low Cost Installation
- Flexible silicone construction allows panel to conform to tank wall. No bonding or heat transfer aids are required.
- High Temperature
- Tank Heating Panels maintain temperatures up to 79°C (175°F) and can withstand exposure to 204°C (400°F).
Subscribe to:
Posts (Atom)