![]() |
Don't let this happen at your plant. |
Main Categories for Industrial Heat Tracing
- Industrial Pipe Tracing Cable
- Industrial Tank and Vessel Heating
- Industrial Snow Melting
- Industrial Roof Gutter Deicing
Responsible facility management includes protecting buildings and equipment against freeze damage. There are many items in any given manufacturing plant to protect, including piping systems, process instrumentation, holding tanks, transfer vessels, and valves. For each of these items, there's a good freeze protection solution to be applied. Here are some of the more common heat tracing products used in these applications.
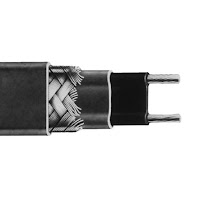
Self-regulating Heat Tracing Cable
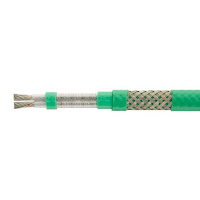
Constant Wattage Heat Tracing Cable
Constant wattage heater cable is ideal for use in maintaining fluid flow under low ambient conditions. The product is used for freeze protection and process temperature maintenance systems such as product pipelines, process water, dust suppression systems, lube oil and condensate return.MI (Mineral Insulated) Cable
MI Cable is a metal sheathed cable that uses a metallic conductor as the heating element. It is custom designed and fabricated for specific applications. MI Cable is a high performance, industrial grade heat tracing cable used for applications requiring high temperature exposure, immunity to stress corrosion, high maintain temperature, under tank heating (cryogenic tanks), high power output, constant power output over entire, rugged cable construction heater length, and extended heater life.It is critical to consider the specific application requirements for any heat tracing application. The following checklist always needs to be clearly understood:
- The mass and material of the item being traced
- Insulation availability - type and thickness
- Temperature to be maintained
- Minimum ambient temperature
- Minimum start-up temperature
- Available supply voltage
- The chemical environment - expose
- Maximum intermittent exposure temperature
- Electrical area classification
Always share your heat tracing requirements and challenges with a process heating specialist. There are many options and product variants from which to choose. A consultation with an expert can help direct you to the safest, most efficient, and most cost effective solution.